Introduction
1. Stamping
Using the latest in manufacturing technology and ˇ§State
of the Industryˇ¨ machinery, every
step in AP's production line is conducted with extreme
precision to ensure all quality standards are achieved
throughout the manufacturing process. Through years
of experience and strict ISO/QS 9000 guidelines, &
now TS16949 compliancy, AP has successfully developed
numerous power-saving processes in our manufacturing
department to maintain quality while containing costs.
The implementation of automated equipment into the
production line and managed by highly trained personnel,
has reduced labor costs while improving the production
cycle time and part quality.
From the initial
stamping process to final part assembly and EDP process,
the entire production procedure was designed as a
Stream Line Process (One Piece Flow). Additionally,
the integration of our ˇ§Double-Bed-Quick Die Change
Machineˇ¨ greatly enhances our ability to achieve a
goal of flexible production schedules, which reduces
the production cost and almost eliminates out of stock
situations.
|
|
|
Double-Bed-Quick
Die Change Machine |
Material Clean |
Surface Inspection |
2. Assembly
In order to enhance the stability of our product quality
and to avoid the potential of man-made errors, AP
has applied the Automatic Jig, the Robotic Spot and
Welding Machine, which essentially eliminates the
variables of manual assembly and makes it easier to
control the assembly process. To ensure our product
quality, each step of the manufacturing process is
subjected to strict testing procedures such as:
Weld Strength Test
Fastener Retention Test
Hood Striker Retention Test
These testing procedures are performed on multiple
samples from each part production lot to ensure consistent
quality throughout a specific lot run as well as a
lot-to-lot comparison. These extensive ˇ§Checks &
Balancesˇ¨ procedures have been conducted to guarantee
our parts will fit on the car promptly and precisely.
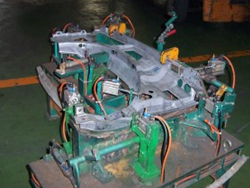 |
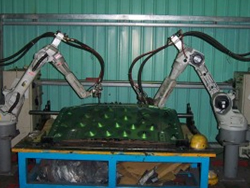 |
Automatic Jig |
Robotic Adhesive
Applying |
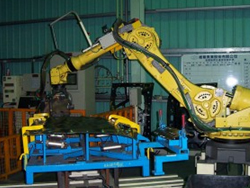 |
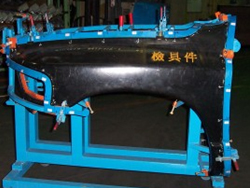 |
Robotic
Spot Welding |
Checking Fixture |
3. EDP
AP has developed and possess the most advanced parts
coating system available with their ˇ§Automated
Electro-Deposition Painting Facilityˇ¨,
and uses a ˇ§Man-Machine
Interface Deviceˇ¨
to monitor all the working processes and conditions,
including where
the human eye cannot see, during
the E.D.P. coating process. In addition to the highly
developed coating system and monitoring devices, AP
applies only the high-tech Radial
Electro-Core Coating, rather
than the traditional Flat Electro-core,
which avoids the unequal coating on a partsˇ¦ surface.
This extensive attention to the coating process allows
us to achieve a superior level of coating quality,
beyond that of any comparable replacement parts.
Finally the Ultrasonic Cleaning Equipment efficiently
cleanses all parts as they pass through the system,
removing all residues, silt or other contaminants
most other systems or manual processes will miss.
All AP-E.D.P. coated products must withstand SAE
recognized 1000 hour Salt Spray or 20 Cycles of Cyclic
Corrosion Tests.
|
|
Automated
Electro-Deposition Painting Facility |
Man-Machine
Interface Device |
|
|
Ultrasonic
Cleaning Equipment |
Awarded by
DANA as 04' Best Supplier of OEM |
4. R&D
AP's reputation has been built on superior engineering
capabilities, intelligent systems and a strong commitment
to R&D. In order to achieve AP's vision of competing
at the highest level by providing our customers with
only the highest quality parts, our R&D team is
dedicated to new product development.
Complying with the ISO9002, ISO/TS16949, CAPA,
and Thatcham standards, AP's Research & Development
team completely evaluates die design specifications
and product materials through strict CAD/CAE/CAM analysis.
Every step in the development of new products including:
Material Testing, Die Design, Die Production Capability,
Production Trial & Evaluation & Mass Production
is handled by professional senior engineers. Once
a part has been fully evaluated and developed for
mass production, it must then be certified by an
INDEPENDENT THIRD PARTY TESTING
FACILITY, ensuring it complies with
the highest quality standards requested in the market.
Through the R&D teamˇ¦s continuous dedication to
study and implementation of the newest technology
in materials and manufacturing processes, we are able
to meet the challenges and demands of todayˇ¦s market
at competitive prices. This constant evolution &
education has allowed AP to accumulated a very rich
experience, not only in Sheet Metal components but
also in the use of newer materials such as: Composite
Materials SMC, GMT, RTM, and RTP Aluminum Products.
AP is proud to be the leading manufacture among our
industry peers in the Research & Development of
new materials and manufacturing technology.
|
|
|
|
|
|
Process Simulation
(CAM) |
Fitting Test in VTF Center
|
|